Operations Management at Maruti Udyog
|
|
ICMR HOME | Case Studies Collection
Case Details:
Case Code : OPEA001
Case Length : 18 Pages
Period : 2003
Organization : Maruti Udyog Limited
Pub Date : 2004
Teaching Note :Not Available Countries : India
Industry : Automobile
To download Operations Management at Maruti Udyog case study
(Case Code: OPEA001) click on the button below, and select the case from the list of available cases:
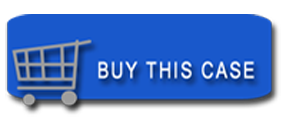
Price:
For delivery in electronic format: Rs. 300;
For delivery through courier (within India): Rs. 300 +Shipping & Handling Charges extra
» Operations Case Studies
» Case Studies Collection
» ICMR HOME
» View Detailed Pricing Info
» How To Order This Case » Business Case Studies » Case Studies by Area
» Case Studies by Industry
» Case Studies by Company
Please note:
This case study was compiled from published sources, and is intended to be used as a basis for class discussion. It is not intended to illustrate either effective or ineffective handling of a management situation. Nor is it a primary information source.
Chat with us

Please leave your feedback
|

<< Previous
Excerpts Contd...
Vendor Management
Vendor management became an important area as Maruti attempted to improve
operational efficiency. Maruti procured components worth about Rs.5,000 crores
every year. The company's top 10 vendors accounted for about 34 % of its
aggregate purchases of components from vendors in India.
Maruti was working on a 3.5% per annum reduction in vendor prices by 2004-2005.
Maruti streamlined the sourcing and stocking of materials and components through
its Delivery Instruction system , one of Suzuki's best practices. This system
provided details of Maruti's component requirements for every 15 days, across
the different variants of the various models, to its vendors. Web initiatives
helped Maruti to bring down procurement time and costs...
|
|
Leveraging Information Technology
When Maruti decided to automate its operations in the early 1990s, there was
no ERP vendor support available in the country. So, the company decided to
do it all by itself. A team of 45 engineers, using a combination of software
from Oracle and Computer Associates, built a variety of applications
covering inventory management, receipts, excise, consumption, production,
sales, invoicing, exports, financial accounting, payroll, and bank
reconciliation. The applications were developed and upgraded on a regular
basis, while the maintenance and administration were outsourced...
|
Looking Ahead
Maruti had plans to raise its operating efficiency to that of Suzuki's
premier plant at Kosai in Japan by 2005. This program had the personal
backing of O. Suzuki, worldwide chairman of Suzuki. Suzuki planned to bring
in new technology from Japan making Maruti capable of full model-development
by 2007. Maruti had plans to export to the Middle East and Far-East Asian
Countries in a big way.
Maruti had set itself the target of wresting a 60% market share of the
country's car market during the period 2003-2006... |
Exhibits
Exhibit I: Maruti Udyog: Major Brands
Exhibit II: Maruti: Manufacturing Process
Exhibit III : Maruti: Raw Materials Expenses
Exhibit IV: Maruti: Employee Productivity
Exhibit V: Maruti: Inventory Management
Exhibit VI: Comparison of Total Inventories
|
|