Sears Logistics Management Practices
|
|
ICMR HOME | Case Studies Collection
Case Details:
Case Code : OPER026
Case Length : 13 Pages
Period : 1993 - 2003
Organization : Sears, Roebuck & Company
Pub Date : 2004
Teaching Note :Not Available Countries : USA
Retail
To download Sears Logistics Management Practices case study
(Case Code: OPER026) click on the button below, and select the case from the list of available cases:
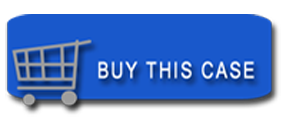
Price:
For delivery in electronic format: Rs. 400;
For delivery through courier (within India): Rs. 400 +Shipping & Handling Charges extra
» Operations Case Studies
» Case Studies Collection
» ICMR HOME
» View Detailed Pricing Info
» How To Order This Case » Business Case Studies » Case Studies by Area
» Case Studies by Industry
» Case Studies by Company
Please note:
This case study was compiled from published sources, and is intended to be used as a basis for class discussion. It is not intended to illustrate either effective or ineffective handling of a management situation. Nor is it a primary information source.
Chat with us

Please leave your feedback
|

<< Previous
Excerpts Contd...
Using Mobile Systems to Manage Logistics
Sears had seven RRCs, which supplied replenishment stocks to more than 870
retail stores all over the US. The RRCs were equipped with automated equipment
like conveyor belts and bar-code scanners. The conveyor belt could move the
goods out at a speed of 10 feet per second. The merchandise flowed in and out of
the seven RRCs 24-hours a day and 7-days a week. In 2001, the RRCs transported
approximately 2.7 billion pounds of goods to various stores.
On an average, one RRC controlled more than 25,000 pallets in a single day and
most of them were stored for not more than a day or two.
|
|
When the goods landed at the RRC, the shipment was
scrutinized to check the type of products supplied and transported to a
warehouse bin, which could be accessed by the replenishment managers. The
replenishment managers scanned the goods to record the consignment and
destination. They also ensured that the quantity and quality of goods had been
supplied correctly...
Recent Initiatives -
Implementing CPFR
Sears shared the benefits of Internet and IT tools with its suppliers to a
very great extent. For instance, Michelin Tires (Michelin) had supplied
automotive tires to Sears for more than three decades. Earlier, the tire
inventory levels of Sears and Michelin were always kept high. Analysts
attributed this to the lack of coordinated planning between Sears and
Michelin and erroneous demand forecasts for tires.
|
To overcome this, Sears embarked on the implementation of the
Collaborative Planning, Forecasting and Replenishment (CPFR) system in
June 2002.
The execution of CPFR comprised four stages. In the first stage,
cross-functional teams of both the companies were trained in the best
practices in CPFR. In the second stage, the IT divisions of both the
companies tracked product information flow and recorded data patterns
that involved product sales history, demand estimations and inventory
levels. In the third stage, the two sides collaborated in selling only
private-label tires. In the fourth stage, the companies broadened CPFR
implementation to accommodate the complete range of Michelin products... |
Exhibits
Exhibit I: Merchandise Division (1994)
Exhibit II: Profit & Loss Statement of Sears (1992-1993)
Exhibit III: Types of Cross Docking
Exhibit IV: Sears Consolidated Income Statements (1994-1998)
|
|