Xerox: The Benchmarking Story
|
|
ICMR HOME | Case Studies Collection
Case Details:
Case Code : OPER012
Case Length : 14 Pages
Period : 1982 - 2002
Organization : Xerox
Pub Date : 2006
Teaching Note : Available
Countries : USA
Industry : Office Automation
To download Xerox: The Benchmarking Story case study
(Case Code: OPER012) click on the button below, and select the case from the list of available cases:
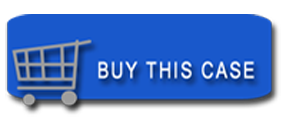
Price:
For delivery in electronic format: Rs. 500;
For delivery through courier (within India): Rs. 500 +Shipping & Handling Charges extra
» Operations Case Studies
» Case Studies Collection
» ICMR HOME
» View Detailed Pricing Info
» How To Order This Case » Business Case Studies » Case Studies by Area
» Case Studies by Industry
» Case Studies by Company
Please note:
This case study was compiled from published sources, and is intended to be used as a basis for class discussion. It is not intended to illustrate either effective or ineffective handling of a management situation. Nor is it a primary information source.
Chat with us

Please leave your feedback
|

<< Previous
Excerpts
About Benchmarking
Benchmarking can be defined as a process for improving performance by constantly
identifying, understanding and adapting best practices and processes followed
inside and outside the company and implementing the results. The main emphasis
of benchmarking is on improving a given business operation or a process by
exploiting 'best practices,' not on 'best performance.'
Simply put, benchmarking means comparing one's organization or a part of it with
that of the other companies. Companies can adopt one or more of the following
types of benchmarking...
|
|
Benchmarking at Xerox
The 'Leadership through Quality' program introduced by Kearns revitalized
the company. The program encouraged Xerox to find ways to reduce their
manufacturing costs. Benchmarking against Japanese competitors, Xerox found
out that it took twice as long as its Japanese competitors to bring a
product to market, five times the number of engineers, four times the number
of design changes, and three times the design costs...
|
Supplier Management System
Xerox found that all the Japanese copier companies put together had only
1,000 suppliers, while Xerox alone had 5,000. To keep the number of
suppliers low, Japanese companies standardized many parts. Often, half
the components of similar machines were identical. To ensure part
standardization, Japanese companies worked closely with their suppliers.
They frequently trained vendor's employees in quality control,
manufacturing automation and other key areas. Cooperation between the
company and the vendor extended to just-in-time production scheduling,
i.e. delivery in small quantities, as per the customer's production
schedule... |
Reaping the Benefits
The first major payoff of Xerox's focus on benchmarking and customer
satisfaction was the increase in the number of satisfied customers. Highly
satisfied customers for its copier/duplicator and printing systems increased by
38% and 39% respectively. Customer complaints to the president's office declined
by more than 60%. Customer satisfaction with Xerox's sales processes improved by
40%, service processes by 18% and administrative processes by 21%...
Exhibits
Exhibit I: Xerox: Operational Data for 1980-1984
Exhibit Ii: Steps Involved in a Typical Benchmarking Process
Exhibit Iii: Comparison Between Old and New Quality Policy of Xerox
Exhibit Iv: Xerox Corporation: Income Statement (1984-1989)
Exhibit V: Guidelines for Successful Benchmarking
|
|