The Six Sigma 'Plus' Quality Initiative at Honeywell
|
|
ICMR HOME | Case Studies Collection
Case Details:
Case Code : OPER024
Case Length : 16 Pages
Period : 2003
Organization : Amazon.com
Pub Date : 2003
Teaching Note : Available
Countries : USA, Global
Industry : Online Retailing
To download The Six Sigma 'Plus' Quality Initiative at Honeywell case study
(Case Code: OPER024) click on the button below, and select the case from the list of available cases:
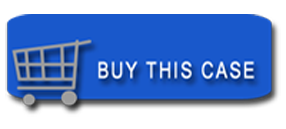
Price:
For delivery in electronic format: Rs. 400;
For delivery through courier (within India): Rs. 400 +Shipping & Handling Charges extra
» Operations Case Studies
» Case Studies Collection
» ICMR HOME
» View Detailed Pricing Info
» How To Order This Case » Business Case Studies » Case Studies by Area
» Case Studies by Industry
» Case Studies by Company
Please note:
This case study was compiled from published sources, and is intended to be used as a basis for class discussion. It is not intended to illustrate either effective or ineffective handling of a management situation. Nor is it a primary information source.
Chat with us

Please leave your feedback
|

<< Previous
Excerpts Contd...
Putting Honeywell back on Track
As a part of the restructuring exercise, Honeywell focused on
five areas - Growth, Productivity, Cash, People and Enablers. Under these areas,
the company mainly focused on cost cuts (through lay-offs and closing
unprofitable businesses), increase in productivity, new product/service
development, growth, effective cash flow management and healthy customer and
employee relationships.
Initiatives such as Six Sigma Plus and DigitalWorks
(formerly Digitization) were classified under the area Enablers.
In mid 2001, Honeywell decided to reinvigorate the Six Sigma Plus exercise. In
line with this, the company put its 3,000 plus base of Black Belts, Master Black
Belts and Lean Experts on priority projects where they could improve processes,
reduce redundancies and cut costs. Apart from this, the company also renewed its
focus on training and certifying hundreds of Black Belts and thousands of Green
Belts every year...
|
|
What Lies Ahead?
In 2003, Honeywell was operating in the following businesses: aerospace
products and services (such as turbofan, turboprop engines, landing systems
and flight safety), control technologies for homes, buildings and industry,
automotive products, and specialty materials (such as semiconductors,
polymers for fibers and electronics and specialty friction products).
|
By early 2003, the company had integrated Six Sigma Plus into
the way its employees thought and worked - thus making Six Sigma Plus an
integral part of the organization's culture - a way of life. In fact, Six Sigma
Plus became more of a mindset than a series of productivity projects.
By now, about 60% of Honeywell management was trained in Six Sigma Plus basics
(i.e. in DMAIC). The company aimed at having 100% of its management trained in
Six Sigma Plus by the end of the year. Apart from this, it also aimed at having
100% of its engineers trained in the Design for Six Sigma (DFSS) program by that
time... |
Exhibits
Exhibit I: A Brief Note on Six Sigma
Exhibit II: The Malcolm Baldrige and EFQM Quality Models
|
|