Supply Chain Restructuring at Sainsbury' Supermarkets Limited | Operations Case Studies
|
|
ICMR HOME | Case Studies Collection
To download Supply Chain Restructuring at Sainsbury' Supermarkets Limited | Operations Case Studies case study
(Case Code: OPER094) click on the button below, and select the case from the list of available cases:
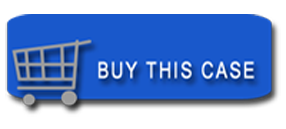
» Operations Case Studies
» Operations Short Case Studies
» View Detailed Pricing Info
» How To Order This Case » Business Case Studies » Case Studies by Area
» Case Studies by Industry
» Case Studies by Company
Please note:
This case study was compiled from published sources, and is intended to be used as a basis for class discussion. It is not intended to illustrate either effective or ineffective handling of a management situation. Nor is it a primary information source.
Chat with us

Please leave your feedback
|

Case Details: |
Price: |
Case Code |
: |
OPER094 |
For delivery in electronic format: Rs.
300; For delivery through courier (within India): Rs.
300 +Shipping & Handling Charges extraThemes
Supply Chain Restructuring |
Case Length |
: |
18 Pages |
Period |
: |
2000-09 |
Organization |
: |
Sainsbury's Supermarkets Limited |
Pub Date |
: |
2010 |
Teaching Note |
: |
Not Available |
Countries
|
: |
UK |
Industry |
: |
Retail |
Abstract:
The case examines the supply chain restructuring process at the UK-based retailer Sainsbury's. Sainsbury's, one of the largest retailers in the UK lost it leadership position to Tesco Plc. during the mid-1990s and continued to lose its market share till the end of 1990s. To address this issue, the company initiated a supply chain restructuring program that replaced the existing depots with highly automated fulfillment factories and consolidation centers to manage transportation of goods in an integrated manner. The existing distribution centers were replaced with fulfillment factories, some of which were fully automated and could handle different kinds of products. However, the implementation of new systems faced several problems and affected the availability of stock in the stores.
|
|
In October 2004, Sainsbury's reported its first ever loss in a history of over 100 years. At this juncture, Justin King, who had assumed the role of CEO of Sainsbury's in March 2004, came out with another supply chain restructuring plan. The plan included the introduction of partially automated systems in the place of fully automated systems.
Several steps were taken to improve the availability of stock, like rolling out hand held devices to report exact stock position, extra manual support, night shifts to stock the stores, etc. With these and other supply chain initiatives, by the end of 2005, the product wastage reduced and instances of
'out of stock' went down. In 2006, most of the issues related to the stock availability were sorted out.
Issues:
» Understand the role of efficient supply chain management in the retail industry.
» Analyze the key operational reasons that led Sainsbury's lose its leadership position in the UK retail industry.
» Evaluate the differences in operational efficiency between the fully automated, partially automated and manual supply chains.
» Study the supply chain restructuring process at Sainsbury's and understand how it helped to turn around the company.
Contents:
Keywords:
Sainsbury's Supermarkets Limited, Supply Chain Restructuring, Supply Chain Automation, Distribution System, Supply Chain Infrastructure,
'7-in-3' Supply Chain Management Program, Automated Fulfillment Factories, Key Performance Indicators, Regional Distribution Centers, Continuous Replenishment, Legacy Systems, Forecasting System Error, Stock File Accuracy, Stock Management Processes, Transport Management System
Supply Chain Restructuring at Sainsbury' Supermarkets Limited
- Next Page>>
|
|