Toyota's Kaizen Experience
|
|
ICMR HOME | Case Studies Collection
Case Details:
Case Code : OPER006
Case Length : 12 Pages
Period : 1990 - 2002
Organization : Toyota
Pub Date : 2003
Teaching Note : Available
Countries : Japan
Industry : Automobiles
To download Toyota's JIT Revolution case study (Case Code: OPER006)
click on the button below, and select the case from the list of available cases:
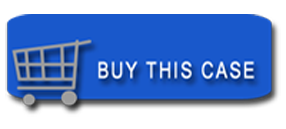
Price:
For delivery in electronic format: Rs. 300;
For delivery through courier (within India): Rs. 300 +Shipping & Handling Charges extra
» Operations Case Studies
» Case Studies Collection
» ICMR HOME
» View Detailed Pricing Info
» How To Order This Case » Business Case Studies » Case Studies by Area
» Case Studies by Industry
» Case Studies by Company
Please note:
This case study was compiled from published sources, and is intended to be used as a basis for class discussion. It is not intended to illustrate either effective or ineffective handling of a management situation. Nor is it a primary information source.
Chat with us

Please leave your feedback
|

<< Previous
Excerpts
About Kaizen & The Toyota Experience
Under Ohno's guidance, Toyota adopted many operational practices that later
became benchmarks for production practices across the global corporate world. It
was one of the first companies in the world to adopt practices such as Kanban,
Jidoka and JIT. However, Kaizen kept TPS, JIT, Kanban, and Jidoka working
smoothly as an interlinked strategic operational plan. Some analysts even felt
that Kaizen was the major contributor to the company's global success.
The founder of the Japan-based 'Kaizen Institute,' Masaaki Imai, defined Kaizen
in his book, 'Kaizen - The Key to Japan's Competitive Success' as, "Kaizen means
continuous improvement in the personal life, home life, social life and working
life."
|
|
When Kaizen is applied to the workplace it means continuous improvement for -
managers and workers. Thus, Kaizen involves everyone in an organization to
make improvements 'without large capital investments.' It can be seen as a
culture of continuous sustained improvement focusing on eliminating waste in
all systems and processes. The Kaizen strategy begins and ends with people.
With Kaizen, an involved leadership guides people continuously to improve
their abilities to meet high quality expectations, low cost and on-time
delivery, which in turn helps the organization gain a competitive edge...
|
The Modification
The modification began with the management deciding
to allow plants to set their own annual production efficiency targets.
The production divisions council, which checked the plants objectives
occasionally modifying them, taking into account the company's profit
targets, replaced the production allowance councils. After approval,
these objectives became the Kaizen norm of each plant in terms of
production efficiency. The method of determining the production
efficiency was altered to make it less constrained as the standard time
was fixed by measuring the time really required for worker's operations
whereas earlier standard time was fixed on the basis of the best
standard time marked in the past... |
Exhibits
Exhibit I: Toyota - Business Results (Consolidated, US GAAP)
Exhibit II: Toyota Production Statistics
|
|