The Ford Production System
|
|
ICMR HOME | Case Studies Collection
Case Details:
Case Code : OPER040
Case Length : 15 Pages
Period : 1991 - 2004
Organization : Ford Motor Company
Pub Date : 2004
Teaching Note :Not Available Countries : USA
Industry : Automobile
To download The Ford Production System case study
(Case Code: OPER040) click on the button below, and select the case from the list of available cases:
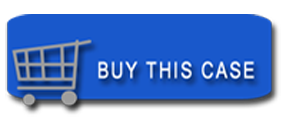
Price:
For delivery in electronic format: Rs. 400;
For delivery through courier (within India): Rs. 400 +Shipping & Handling Charges extra
» Operations Case Studies
» Case Studies Collection
» ICMR HOME
» View Detailed Pricing Info
» How To Order This Case » Business Case Studies » Case Studies by Area
» Case Studies by Industry
» Case Studies by Company
Please note:
This case study was compiled from published sources, and is intended to be used as a basis for class discussion. It is not intended to illustrate either effective or ineffective handling of a management situation. Nor is it a primary information source.
Chat with us

Please leave your feedback
|

<< Previous
Introduction Contd...
The reengineering effort was known as Ford Production System (FPS). Modeled on
the famous Toyota Production System, FPS aimed at developing and applying the
best practices in automobile manufacturing. FPS involved the implementation of
techniques used in lean manufacturing.
Apart from using advanced technologies to help reduce waste, FPS emphasized the
human aspects as well. It required its employees to form teams called work
groups, and empowered managers to take work decisions without wasting time. Ford
implemented the FPS in its plants across the world and realized improved
productivity levels and financial performance.
|
|
Background Note
Ford was established by Henry Ford on June 16, 1903, with an initial investment
of $100,000. Ford initially produced cars using the Craft Production System
(CPS). Under CPS, all cars were produced with same basic chassis and engine
but with different designs according to individual customer preferences and
tastes. However, in CPS, the manufacturing costs were high and did not
decline with greater volumes.
|
Initially,
at the Ford factory, the assembly stands on which a whole car was
assembled by one fitter (assembler) were used. A Ford worker assembled a
large part of a car before proceeding to the next car. The fitters
performed the same set of activities repetitively at their fixed
assembly stands.
Workers procured the necessary parts, so that they could fit and then
bolt them at the appropriate places. Later, to increase the efficiency
of the process, each workstation was supplied with the required parts.
This allowed the assemblers to remain at a given place throughout the
day. |
In 1908, Ford introduced the mass-production system for the
production of Model T5. The novelty in
this system was that the parts were standardized and fixing them on became much
easier. To enable the parts to be used interchangeably, Ford standardized the
gauging system6 throughout the production
process...
Excerpts >>
|
|